The Benefits of O-Ring & Seal Upkeep and Replacement in Hot Runner and Injection Molding Systems
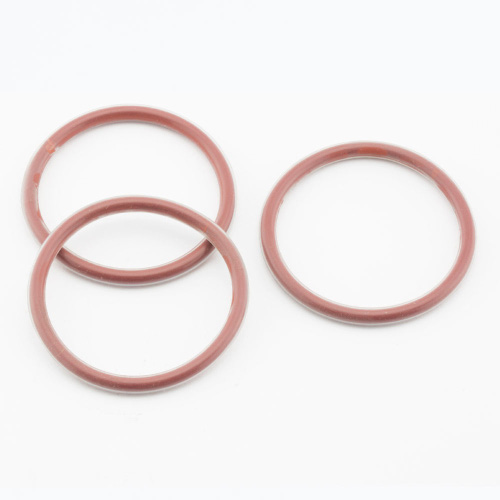
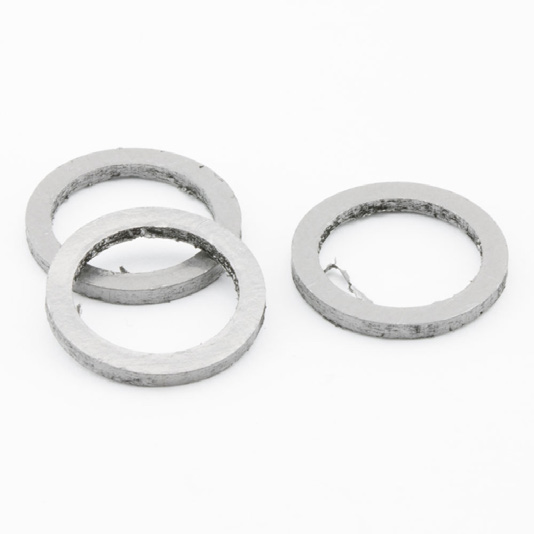
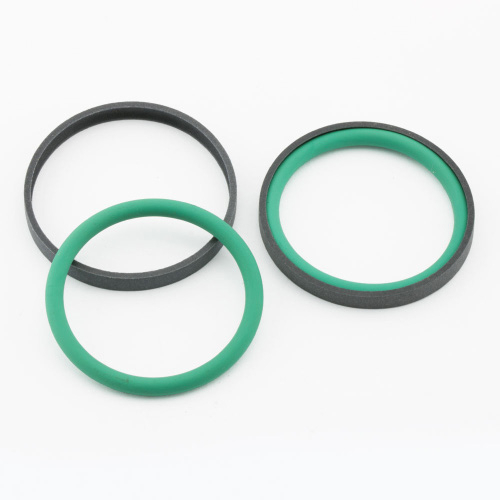
Injection molding, especially when using hot runner systems, is essential for high-volume, complex, and precise plastic part production. While hot runner systems can streamline production by reducing waste and cycle times, they also bring their own unique set of maintenance challenges. One of the critical aspects of this maintenance is the upkeep and replacement of O-rings and seals, which play a vital role in the functionality and efficiency of hot runner systems.
Why O-Ring & Seal Maintenance is Essential
O-rings and seals are small but crucial components in hot runner and injection molding systems. Their primary function is to prevent leaks by maintaining tight seals within the system’s components, even under high temperatures and pressures. When functioning optimally, they ensure consistent mold temperature, maintain material flow, and prevent the unwanted mixing of plastics or degradation of materials. However, due to their exposure to extreme operating conditions, these parts are subject to wear, hardening, and potential failure.
In a hot runner system, a faulty O-ring or seal can lead to several issues:
- Material Leakage: Poor seals can allow molten plastic to leak into areas where it doesn’t belong, leading to contamination and defects in the molded parts. This not only impacts product quality but can also require extensive cleanup and mold downtime.
- Inconsistent Temperature: Seals play an essential role in maintaining thermal consistency. A compromised O-ring or seal can allow cold spots or temperature fluctuations that disrupt material flow, leading to part inconsistencies and defects.
- Premature Equipment Wear: When seals and O-rings aren’t maintained, they can cause damage to other components. Material leakage can lead to degradation of nearby parts, including hot runner nozzles, heaters, and connectors, which can result in unplanned downtime and costly repairs.
Polymer Cleaning Technology, a leading provider of replacement O-rings and seals, emphasizes that consistent upkeep of these parts not only protects your investment in the hot runner system but also optimizes productivity and product quality.
Key Benefits of Regular O-Ring & Seal Replacement
While many manufacturers may be tempted to push their hot runner systems to their limits, proactive maintenance—especially for O-rings and seals—offers several benefits that make this upkeep worthwhile:
1. Enhanced Product Quality
Damaged or worn seals can allow the introduction of unwanted contaminants into the mold cavity, leading to defective or compromised parts. Small imperfections can go undetected until later stages, potentially leading to costly recalls. Consistently maintaining and replacing O-rings and seals ensures that no unwanted material enters the mold, preserving the quality and reliability of each part produced.
2. Reduced Downtime and Maintenance Costs
Failed O-rings and seals can cause system leaks, clogging, and contamination issues, all of which require extensive cleaning and system downtime to fix. By performing regular inspections and proactively replacing worn seals, you can prevent these issues from escalating, reducing both downtime and the frequency of major maintenance activities. HotRunnerSpares.com recommends regular maintenance checks to identify wear before it becomes a costly problem.
3. Optimized Cycle Times and Efficiency
A properly sealed hot runner system maintains consistent temperature and pressure, allowing material to flow evenly and preventing variations that can lead to defective parts. When seals and O-rings are functioning optimally, they help streamline cycle times, allowing manufacturers to produce more parts in less time. This efficiency is critical for meeting high production demands and maintaining cost-effectiveness.
4. Extended System Lifespan
Hot runner systems are a significant investment, and replacing them due to preventable wear or damage is costly. Ensuring that O-rings and seals are regularly maintained and replaced as needed can prevent damage to other components. Seals that work effectively minimize the wear and tear on heaters, manifolds, and nozzles, helping to extend the life of the entire system.
Practical Tips for O-Ring & Seal Maintenance
Here are some best practices to help manufacturers ensure optimal performance of their hot runner systems:
- Conduct Regular Inspections: Periodic inspections of the hot runner system should include checking seals and O-rings for signs of wear, hardening, or cracking. These checks allow you to catch potential issues before they escalate.
- Replace During Scheduled Maintenance: Incorporate seal and O-ring replacement into scheduled maintenance activities to avoid unscheduled downtime. This proactive approach keeps systems running efficiently and minimizes production interruptions.
- Choose High-Quality Replacements: Selecting high-quality O-rings and seals is crucial for maintaining system integrity. HotRunnerSpares.com provides a range of O-rings and seals designed to withstand the high pressures and temperatures typical of hot runner systems, ensuring that replacements last as long as possible under challenging conditions.
- Track Replacement Frequency: Documenting the frequency of O-ring and seal replacements can help identify trends in wear and predict when future replacements might be needed, enabling better planning for maintenance and parts inventory.
Source O-Rings and Seals from Trusted Suppliers
Not all O-rings and seals are created equal. For a hot runner system to run smoothly, replacement parts must meet high standards of durability and heat resistance. Choosing a trusted supplier like Polymer Cleaning Technology can help ensure that you’re getting parts specifically designed for the unique demands of injection molding.
HotRunnerSpares.com, powered by PCT, offers a range of O-rings and seals that are manufactured to withstand the intense conditions within hot runner systems, including high temperatures and chemical exposure. Sourcing from a specialized distributor ensures compatibility and reliability, reducing the risk of failures and minimizing potential downtime.
Conclusion
Regular maintenance and replacement of O-rings and seals are essential for the smooth operation of hot runner and injection molding systems. These small yet crucial components protect the integrity of the system, enhance product quality, and extend the life of valuable equipment. Proactively managing the upkeep of O-rings and seals—by scheduling regular inspections, choosing quality replacements, and sourcing parts from trusted suppliers like Polymer Cleaning Technology—can significantly improve the efficiency and reliability of injection molding operations.
Investing time and resources into seal and O-ring maintenance is a proactive step that helps ensure production consistency, minimize costly downtime, and keep your systems running smoothly for years to come. By integrating these practices into a robust maintenance program, manufacturers can protect their investments and maximize the productivity of their hot runner systems.
Verified resources provide in-depth information on the technical and operational importance of O-ring and seal maintenance in hot runner and injection molding systems, alongside broader discussions of system efficiency, preventive maintenance, and quality control:
- Books and Technical Manuals on Injection Molding and Hot Runner Systems
- “Injection Molding Handbook” by Dominick V. Rosato et al.
- “Runner and Gating Design Handbook: Tools for Successful Injection Molding” by John P. Beaumont
- “Injection Molding Advanced Troubleshooting Guide: The 4M Approach” by Randy Kerkstra and Chris Rauwendaal
- Peer-Reviewed Journals and Articles
- “Design and Optimization of Injection Molds” (Journal of Manufacturing Processes)
- “Maintenance in Injection Molding: Reliability and Efficiency Improvement” in the Journal of Cleaner Production
- Industry Standards and Technical Guides
- Society of Plastics Engineers (SPE) Technical Papers
- ASTM Standards for Rubber and Elastomeric Seals (e.g., ASTM D2000)
- White Papers and Reports from Hot Runner Manufacturers and Suppliers
- Husky Injection Molding Systems White Papers
- Mold-Masters Technical Papers
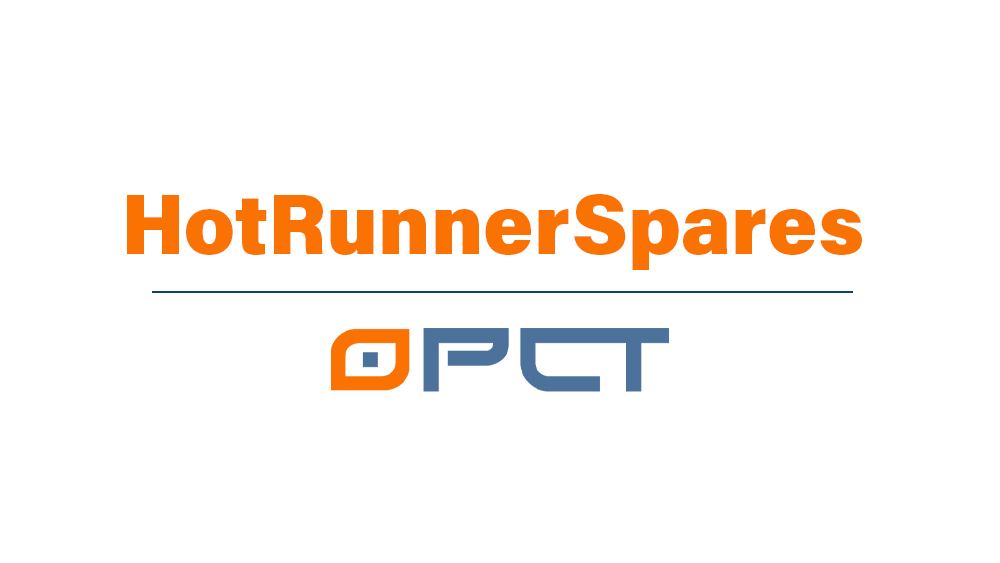
Hot Runner Repairs & Manifold Cleaning by PCT available at HotRunnerManifoldCleaning.com
Find this information useful? Share with friends & colleagues:
Contact Information:
Polymer Cleaning Technology, Inc.
[email protected]
+1 (908) 281-0055