The Importance of Hot Runner Manifold Cleaning and Maintenance for Operational Efficiency
In the world of plastic injection molding, hot runner systems play a critical role in streamlining the production process, minimizing waste, and increasing product quality. A key component of this system is the hot runner manifold, which distributes molten plastic through various channels into the mold cavities. Keeping hot runner manifolds clean and well-maintained is essential to ensure optimal efficiency and extend the lifespan of the equipment. This article delves into the importance of hot runner manifold maintenance, best practices for keeping these systems in top shape, and highlights leading brands that exemplify innovation in hot runner injection molding systems.
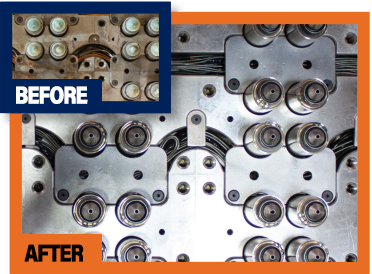
For same-day quotes on all Hot Runner Cleaning, Hot Runner Repair, Nozzle & Power Lead Repair and more Hot Runner Services visit HotRunnerManifoldCleaning.com and contact Polymer Cleaning Technology today!
What is a Hot Runner Manifold?
A hot runner manifold is a heated component within a hot runner injection molding system that delivers molten plastic to mold cavities. Unlike cold runner systems, where plastic solidifies within the runners, a hot runner system keeps the material in a molten state, which enables faster cycle times, reduces material waste, and improves production consistency. Manifolds are central to hot runner systems, allowing the plastic to flow evenly to the mold cavities and enabling the creation of high-quality, dimensionally accurate parts.
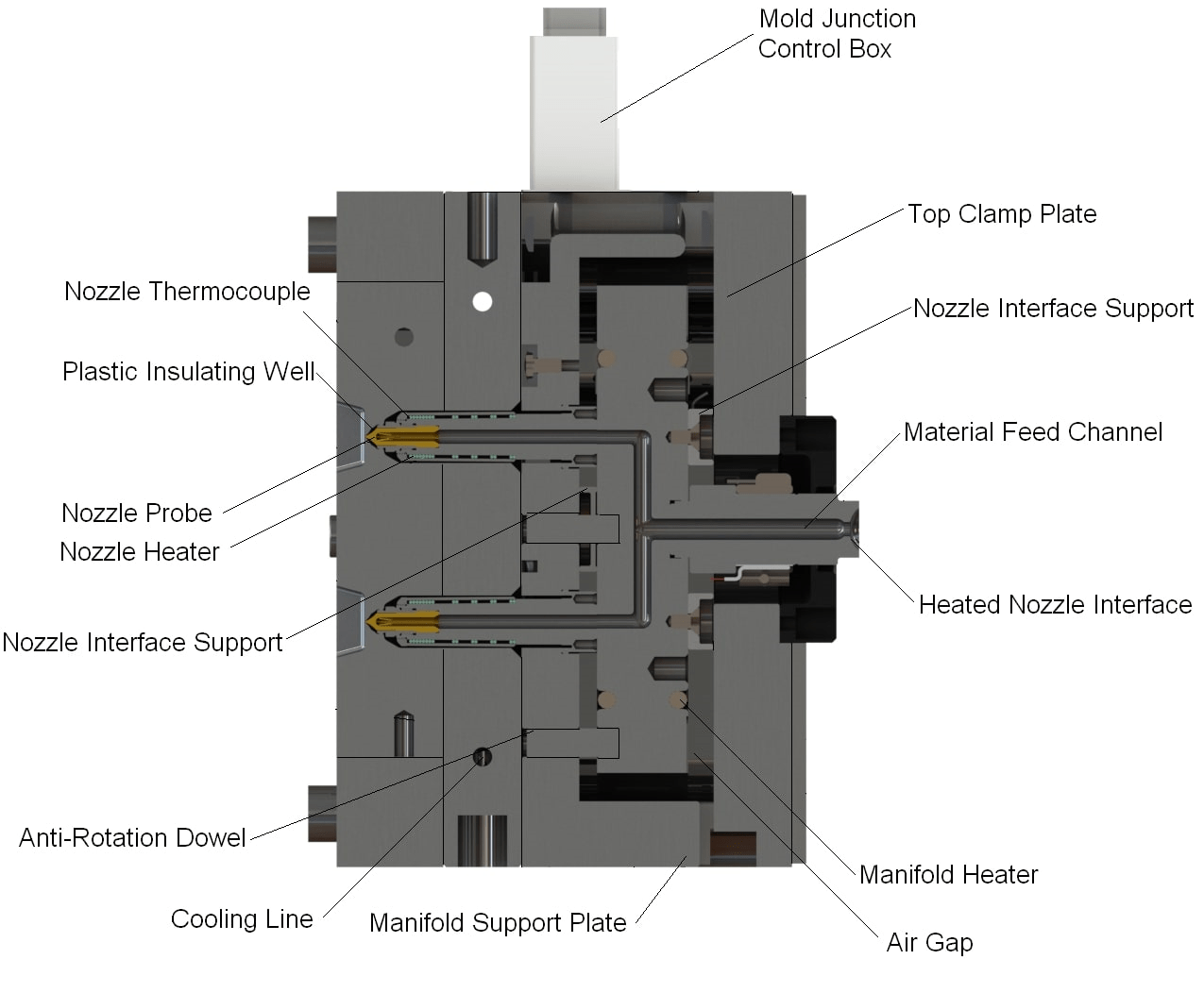
Importance of Hot Runner Manifold Maintenance
Hot runner manifolds are essential for maximizing productivity and minimizing downtime in injection molding operations. Neglecting maintenance can lead to several issues, including:
Reduced Material Flow: Residue buildup or blockages can restrict plastic flow, causing quality issues and production delays.
Increased Energy Consumption: If the manifold’s heating elements work harder due to blockages or residue, energy costs will rise.
Downtime and Costly Repairs: Clogged or malfunctioning manifolds can cause expensive production stoppages and may require complex repairs or replacements.
Routine hot runner manifold maintenance and general hot runner repair helps to avoid these issues, ensuring that the system runs efficiently and continues to produce high-quality parts.
Best Practices for Maintaining Hot Runner Manifolds
Regular Cleaning and Inspection
- Residue buildup inside manifolds is a common issue that can lead to flow restrictions and color contamination. Cleaning out these residues periodically ensures that the manifold functions optimally.
- A visual inspection should be done regularly to check for signs of wear or potential blockages. Clean manifolds at least once per production cycle or after switching materials or colors.
Preventing Material Degradation
- High temperatures in hot runner manifolds can cause certain plastics to degrade over time. If material degradation occurs, it can form carbon deposits, leading to mold damage or defects in the final product.
- Manufacturers suggest maintaining temperature control carefully to prevent overheating, as well as regularly purging the system to remove degraded plastic.
Routine Temperature Monitoring and Calibration
- Heat distribution is crucial for the efficient operation of hot runner systems. Uneven heating can lead to material flow inconsistencies, which may cause defects.
- Most hot runner systems come with advanced sensors and controllers for precise temperature management, which helps manufacturers keep temperature profiles consistent across production runs.
Utilizing Specialized Cleaning Tools and Techniques
- Using specialized tools like purging compounds is beneficial for cleaning out the manifold and preventing contamination. Purging compounds help dissolve residual material, making it easier to remove.
- Manufacturers recommend purging compounds designed specifically for hot runner systems to ensure thorough and safe cleaning without damaging the equipment.
Monitoring for Wear and Tear
- Over time, components within the manifold, such as seals and thermocouples, may wear out and require replacement.
- Replacing these parts on a preventative schedule, rather than reacting to failures, is a crucial practice for minimizing downtime.
Benefits of Well-Maintained Hot Runner Manifolds
The benefits of maintaining a clean and properly functioning hot runner manifold go beyond operational efficiency. Here are some additional advantages:
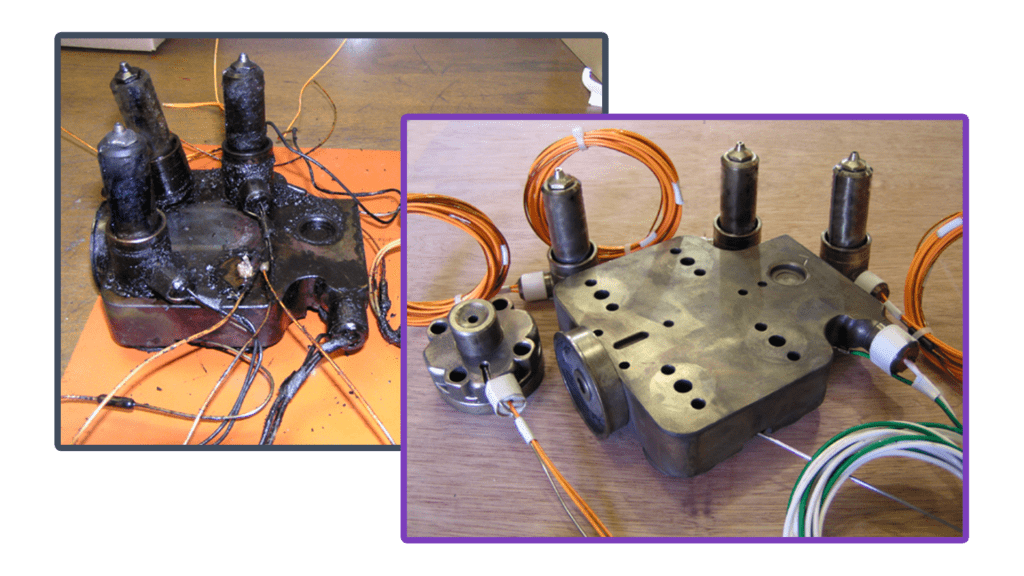
Enhanced Product Quality: Properly maintained manifolds help ensure that the plastic flows uniformly, resulting in fewer defects and higher-quality products.
Reduced Downtime: Regular maintenance minimizes the risk of unexpected breakdowns, allowing for a smoother production process and reducing the likelihood of costly interruptions.
Energy Savings: Clean manifolds operate more efficiently, reducing the amount of energy required to keep the material at the correct temperature, leading to energy savings over time.
Extended Equipment Lifespan: By following a regular maintenance schedule, manufacturers can extend the lifespan of their hot runner systems, maximizing the return on their investment.
Conclusion
Keeping hot runner manifolds clean and well-maintained is essential for any injection molding operation that prioritizes efficiency, product quality, and cost-effectiveness. Leading brands offer systems with advanced monitoring and maintenance capabilities, enabling manufacturers to take a proactive approach to manifold care.
By following best practices for cleaning, temperature management, and wear monitoring, businesses can ensure that their hot runner systems continue to perform at a high level, meeting production demands and maintaining competitive advantage.

These additional resources provide in-depth information on hot runner injection molding and practical guidance on manifold maintenance, helping operators and technicians apply best practices in their facilities:
- Bryce, D. M. (1999). Plastic Injection Molding: Manufacturing Process Fundamentals. Society of Manufacturing Engineers.
- Bozzelli, J. (2022). Injection Molding Reference Guide, Gardner Business Media.
- Technical manuals and documentation from leading OEM companies
(HUSKY, Mold-Masters, Männer, Yudo, Sacmi, Sipa, Synventive, Milacron, Nissei, MHT, and more)
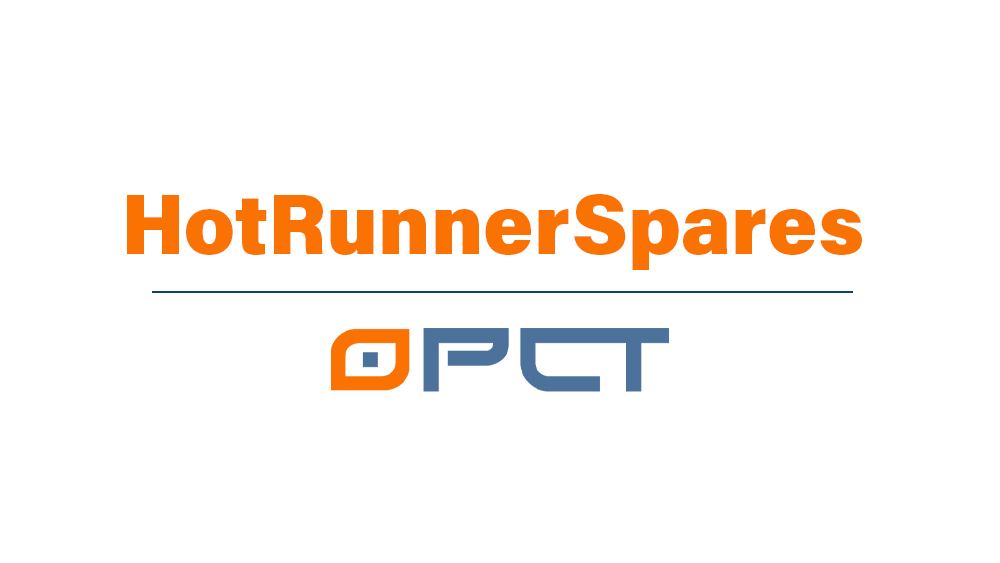
Hot Runner Repairs & Manifold Cleaning by PCT available at HotRunnerManifoldCleaning.com
Find this information useful? Share with friends & colleagues:
Contact Information:
Polymer Cleaning Technology, Inc.
[email protected]
+1 (908) 281-0055