Understanding Hot Runner Valve Pins in Injection Molding Systems
Valve pins are a vital component in hot runner injection molding systems, enabling manufacturers to produce high-quality plastic parts with precision and efficiency. These small yet crucial components directly influence the molding process’s success, ensuring consistent performance and minimizing waste.
Polymer Cleaning Technology is the largest provider of Hot Runner Spare Parts including Valve Pins for all Hot Runner Systems. Standard Valve Pins available for same day shipping. Our reverse engineering & high-precision grinding capabilities offer OEM quality at substantial savings.
Same-Day Shipping Available for Standard Parts!
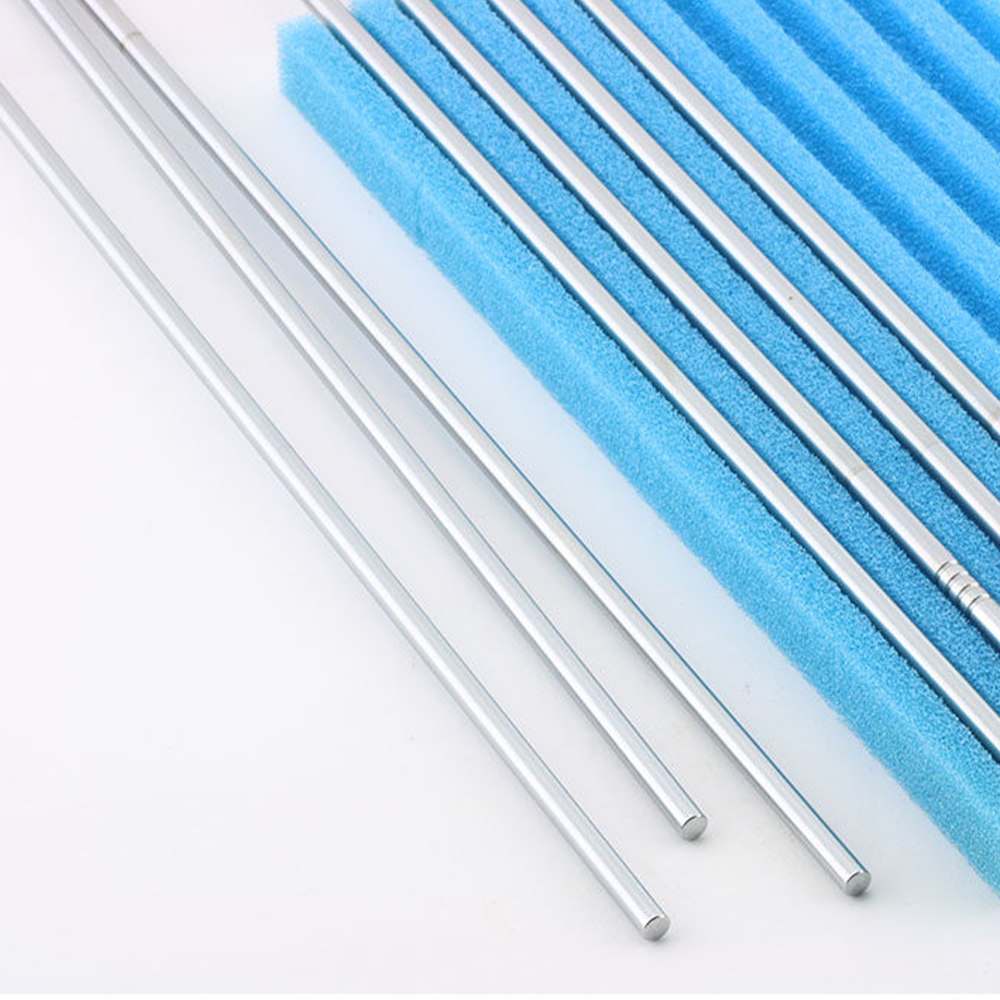
This guide delves into the role of hot runner valve pins in plastic injection molding, explores the differences between Standard, Shallow Groove, and Deep Groove valve pins, and highlights the various styles of valve pins available for customization.
The Role of Hot Runner Valve Pins in Injection Molding
Hot runner systems are widely used in injection molding to streamline the delivery of molten plastic into molds. Within these systems, hot runner valve pins play a critical role by regulating the flow of molten material through the gate and into the mold cavity.
Valve pins in injection molding systems help achieve:
Precision and Control: By opening and closing the gate at specific intervals, valve pins ensure consistent filling and minimize defects like sink marks or flash.
Cycle Time Efficiency: With precise gating, hot runner valve pins reduce the cycle time, increasing production speed.
Waste Reduction: By optimizing the gate’s operation, valve pins eliminate excessive material leakage, reducing scrap and improving sustainability.
Grooved Valve Pins: Key Differences
Valve pins are tailored to meet specific application requirements. Among the most common designs are Standard, Shallow Groove, and Deep Groove. Each type offers unique benefits based on the complexity of the mold and material being used.
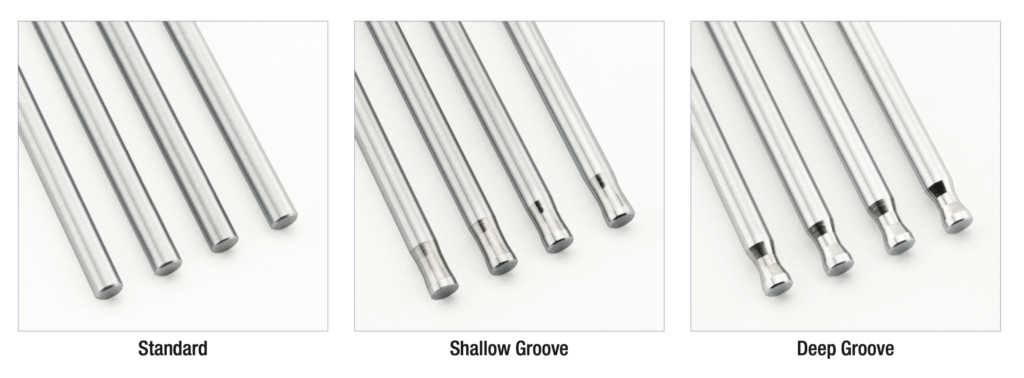
1. Standard
Overview: Standard pins are the most versatile and widely used type.
Features: They have a uniform surface and are suitable for general-purpose applications where standard gating precision is sufficient.
Advantages: Cost-effective, easy to maintain, and compatible with a wide range of materials.
2. Shallow Groove
Overview: Shallow groove pins are designed to enhance material flow and reduce friction.
Features: These pins feature small, shallow grooves along their surface, which facilitate better material distribution in molds with complex geometries.
Advantages: Ideal for applications requiring a smooth finish and precise cavity filling.
3. Deep Groove
Overview: Deep groove pins are specialized for high-flow applications and abrasive materials.
Features: They have deeper grooves, providing increased material flow capacity and better wear resistance.
Advantages: Perfect for high-volume production or when using challenging plastics such as glass-filled materials.
Main Styles of Injection Molding Valve Pin
Hot runner systems are not one-size-fits-all. Depending on the mold design and manufacturing requirements, valve pins can be customized in various styles, including:
Flat Tip Pins: For even material distribution and general-purpose applications.
Conical Tip Pins: Designed to enhance sealing and reduce gate vestige.
Tapered Groove Pins: Ideal for improving flow dynamics in molds with intricate shapes.
Custom Designs: Tailored to meet unique operational needs, offering maximum precision and compatibility.
Reverse Engineering and Cost-Effective Solutions
When it comes to maintaining or upgrading your hot runner system, finding cost-efficient yet high-quality solutions is essential. Polymer Cleaning Technology excels in reverse engineering hot runner parts, including Husky valve pins and Mold Masters valve pins.
With state-of-the-art precision grinding techniques, Polymer Cleaning Technology produces injection molding valve pins that match OEM quality while offering substantial cost savings. Whether you require replacements for standard designs or custom configurations, their expertise ensures seamless integration into any hot runner system.
Conclusion
Valve pins are essential in hot runner injection molding systems, dictating the precision, efficiency, and quality of the final product. Understanding the differences between Standard, Shallow Groove, and Deep Groove valve pins, as well as the range of available styles, can help manufacturers select the best components for their needs.
By partnering with experts like Polymer Cleaning Technology, you can ensure that your hot runner valve pins—whether they’re Husky valve pins, Mold Masters valve pins, Manner Valve Pins or custom designs—meet the highest standards while optimizing production costs. Elevate your injection molding processes with precision-engineering that guarantees reliable performance and exceptional results.
This brief guide serves to help manufacturers make informed decisions, ensuring efficiency and quality in every cycle. For additional information on Injection Molding Valve Pins, and their role in optimizing system efficiency, visit these verified resources:
- “Visualization of Cascade Injection Molding in Hot-Runner System” (AIP Publishing)
This study explores the flow dynamics within hot runner systems, emphasizing the critical role of valve pins in controlling material flow to reduce defects like weld lines and pressure loss. It highlights the advanced control of valve pins to manage melt flow behavior during sequential gate opening, essential for high-quality production in injection molding.
AIP Publishing - “Influence of Different Hot Runner Systems on Mechanical Properties” (MDPI)
This paper investigates the mechanical and structural impacts of hot runner systems, including valve gate systems, on molded parts. It underscores how valve pin designs influence behavior, contributing to the precision and performance of molded products.
Access the full article MDPI - “Revisiting Some Hot Runner Fundamentals” (MoldMaking Technology)
This resource explains the operational principles of hot runners, including valve pin functions, such as controlling resin flow and enhancing mold insights into reducing cycle times and waste, which are integral advantages of properly engineered valve pin systems.
MoldMaking Technology
These resources collectively demonstrate the engineering significance of valve pins in enhancing injection molding precision, reducing material waste, and improving product quality. They also provide academic and technical perspectives on advancements in hot runner technologies.
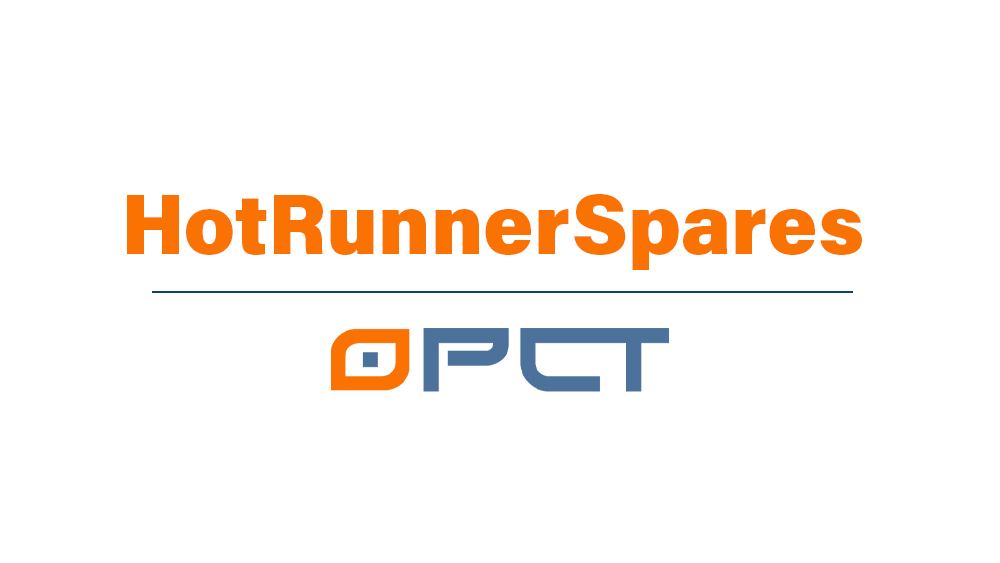
Hot Runner Repairs & Manifold Cleaning by PCT available at HotRunnerManifoldCleaning.com
Find this information useful? Share with friends & colleagues:
Contact Information:
Polymer Cleaning Technology, Inc.
[email protected]
+1 (908) 281-0055